Notre technologie
Parce que nos processeurs Microfluidizer sont utilisés pour traiter des demandes similaires, quoiqu’avec des résultats radicalement différents, ils sont souvent confondus à des homogénéisateurs à hautes pressions. En réalité, l’innovation Microfluidics transforme l’horizon de l’industrie du traitement des fluides.
La technologie Microfluidizer
Créer, générer de minuscules particules avec une granulométrie homogène et uniforme, représente un réel enjeu industriel et une véritable problématique. Et bien sûr, la réussite dans le laboratoire est seulement valable si le processus peut être répété de façon fiable en production.
La technologie innovatrice des appareils Microfluidizer est utilisée pour les émulsions, les dispersions, la désagglomération, l’encapsulation ainsi que pour la rupture des cellules, et représente une alternative très attractive par rapport aux méthodes conventionnelles.
Vous pouvez désormais effectuer des formulations uniformes et reproductibles qui seront faciles à transposer de l’échelle du laboratoire à celle de la production.
Grâce à la technologie Microfluidizer, votre produit est à chaque fois intégralement exposé à des conditions de traitement identiques dans la chambre d’interaction à géométrie fixe
Fonctionnement
Le processeur Microfluidizer agit comme une grande pompe qui force la matière à travers un très petit orifice. Les pressions de fonctionnement commencent a environ 34 Bar et peuvent aller jusqu’à 2750 bars. La pression varie en fonction de chaque application afin d’ obtenir la distribution granulométrique souhaitée.
L’échantillon est d’abord versé dans l’entrée du réservoir. La pompe intensificatrice a deux mouvements: Aspiration et compression.Pendant la course d’aspiration, une partie de l’échantillon est aspiré dans le processeur grâce à un sens unique (Soupape). La course de compression suit et va pousser cette portion de l’échantillon à travers la chambre d’interaction puis à travers le serpentin de refroidissement pour être refroidi. L’échantillon est alors recueilli.
Chambre d’interaction
La chambre du processeur Microfluidizer est essentiellement un micro réacteur continu qui utilise le mélange turbulent, la dissipation d’énergie localisée , et une géométrie fixe pour créer une pression uniforme .
A l’intérieur de la chambre d’interaction, le produit est soumis à la fois à des forces d’impacts et de cisaillement très élevés qui conduisent à la réduction de taille de particule / Broyage de cellules.
Les micro canaux peuvent mesurer jusqu’a 50 microns, ce qui crée des volumes micros qui, collectivement, connaissent un profil de pression jusqu’à 2750 bar et donc une application uniforme de cisaillement.
Les forces d’impact se produisent quand le produit se déplaçant à des vitesses atteignant plusieurs centaines de m/s, frappe les parois de la chambre, ou bien encore lorsque de flux de produits se percutent.
Cependant, le facteur qui contribue le plus à la réduction de taille de particules / broyage de cellules est le cisaillement.
Le design spécifique et unique de nos chambres d’interaction permet en l’occurrence d’atteindre des taux de cisaillement bien plus élevés qu’avec n’importe quelle autre technologie.
If Velocity Maximum (Vmax) = 20.000 mm/s
Velocity at Wall (Vwall) = 0
Then Average Shear = 20.000 mm/s / 0.05 mm
Le cisaillement provient des différentiels de vélocité qui se produisent au sein de la chambre d’interaction.
Plus précisément et en assumant que le flot du produit circulant dans la chambre d’interaction est laminaire, le taux de cisaillement résulte de la différence entre la vélocité au centre du conduit de la chambre (vélocité max.) et celle en bordure de parois (vélocité min. du fait des frictions générées par le contact), divisé par la distance séparant la paroi du centre.
Du fait que dans la réalité le flot est non pas laminaire mais turbulent, les forces de cisaillement produites sont encore plus importantes.
Fonctionnement et taux de cisaillement
Le facteur prédominant qui contribut aux réductions des tailles de particules est le taux de cisaillement.
Les processeurs Microfluidizer sont « l’étalon-or » dans l’industrie pour des applications qui nécessitent un fort cisaillement. Les fluides à l’intérieur des chambres peuvent se déplacer à des vitesses allant jusqu’à 500 m / s, plus rapide que la vitesse du son (343 m/s). La dimension minimum de l’intérieur de la chambre peut atteindre la finesse de 50 µm.
Ce schéma diffusé dans le magazine » Chemical Engineering » montre les taux de cisaillements générés par différentes technologies. Il illustre clairement que la technologie de nos Microfluidizer génère le plus haut taux de cisaillement du marché.
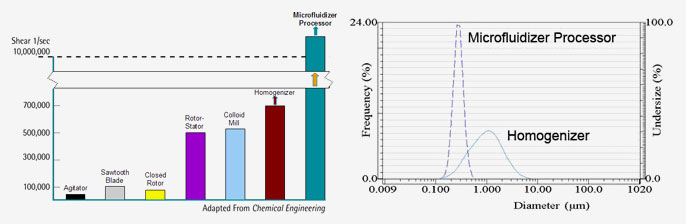
Schéma 1 : Comparaison du taux de cisaillement de notre Microfluidizer avec les autres technologies .
Schéma 2 : Distribution la plus étroite de la taille de particule
Les autres technologies traditionnelles à « cisaillement élevé » ne peuvent pas être comparée avec le processeur Microfluidizer .
La clé est l’orifice à géométrie fixe qui ne change pas avec une pression accrue. Contrairement à d’autres technologies, le processeur Microfluidizer maintient un flux d’alimentation constant généré par une géométrie fixe, produisant ainsi l’impact nécessaire pour obtenir un cisaillement élevé et atteindre une distribution granulométrique optimale (polydispersité index).
Pression
La pression appliquée est le mécanisme qui propulse l’échantillon à travers la chambre et qui réalise la réduction des particules (cisaillement), l’encapsulation, la désagglomération, etc
La pression est l’un des moteurs pour le cisaillement et le débit volumétrique. Augmenter la pression va augmenter le taux de cisaillement et augmenter la quantité d’échantillon qui peut être traitée dans un temps donné.
Toute notre gamme de matériel ne fournit pas le même taux de cisaillement. Les produits alimentaires, par exemple, nécessitent moins de cisaillement pour un traitement optimal.
Nombre de passes
Les processeurs peuvent être utilisés pour traiter à la fois des opérations en lots et des opérations continues. Un échantillon peut être traité en une seule «passe» par la chambre ou de façon continue en plusieurs passes. Laisser passer plusieurs fois le produit à travers la chambre augmentera le
temps d’exposition. Si la taille des particules désirée n’ a pas été obtenue après le premier passage, les passages suivants permettront d’ atteindre la taille et la distribution désirées.